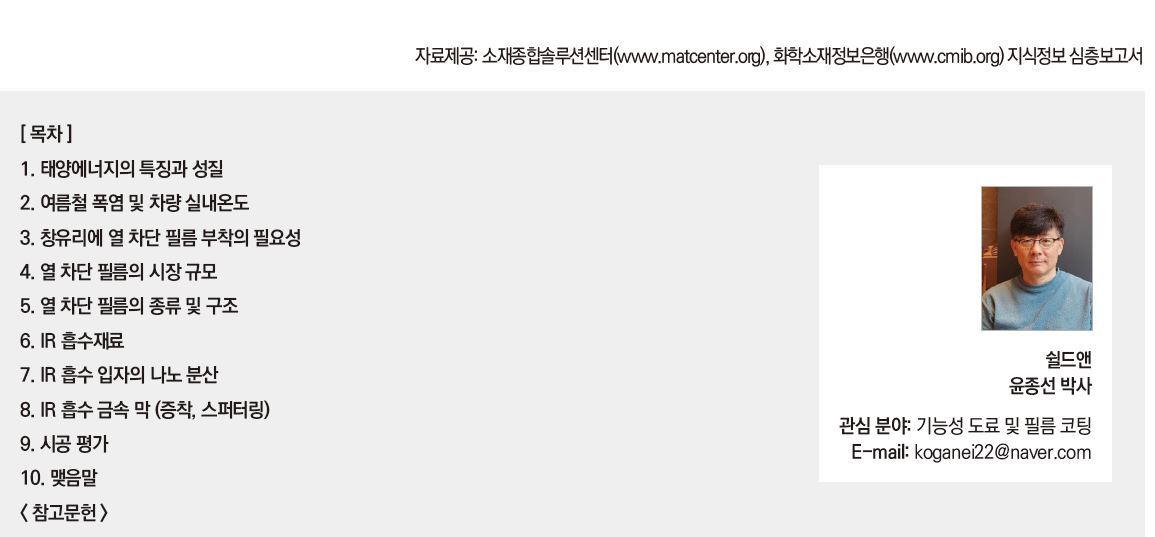
1. 태양에너지의 특징과 성질
태양으로부터 방출되는 에너지양은 일 년 내내 거의 일정하지만, 지구의 공전궤도가 타원형이고 지축이 기울어진 천문학적 요인에 의해 지구가 받는 태양복사 에너지양은 계절에 따라 변화하고 있다. 태양과 지구의 평균 거리는 약 1.5×108km로, 이 거리가 1AU(AU: Astronomical Unit)이다. 지구가 가장 태양에 가까워지는 곳은 근일점이고, 반대로 멀어지는 곳은 원일점이라 한다. 방사강도는 거리의 제곱에 반비례하며 거리가 멀어질수록 작아진다.
지구는 태양 주위를 1년에 걸쳐 한 바퀴 도는 공전운동 외에 약 24시간 주기로 자전운동을 하고 있다. 이때 지구의 지축이 공전 면에 대해 약 66.5°로 기울어져 있기 때문에 북반구의 겨울은 태양으로부터 멀어지는 방향으로 기울고, 반대로 여름은 태양에 가까워지는 방향으로 기울어진다. 지표면에서의 방사강도는 태양이 수평면과의 사이에 이루는 각도의 사인에 비례하기 때문에 태양의 남중고도가 높아지는 여름에 북반구의 방사강도가 커진다.
태양이 방출하는 전자파를 태양복사라 한다. 태양복사는 태양의 표면온도가 약 5,540℃인 높은 온도에서 방출하는 복사에너지로 대기권 밖의 태양광 스펙트럼은 태양 표면의 복사 스펙트럼과 매우 유사한 형상을 나타내고 있다.
그리고 태양복사 에너지는 지구에 도달한 후 공기, 구름, CO₂ 등에 의해 흡수·산란하기도 하며 지표에 도달할 때까지 감쇠·확산하기 때문에 그림 2과 같은 분포가 된다. 생명에 해로운 자외선 등 300㎚ 이하의 파장대는 대기권 밖의 태양광 스펙트럼에는 분포를 보이지만, 오존층에 의한 흡수로 지표에는 도달하지 않는다.
태양에서 우주공간을 거쳐 지구에 도달하는 태양의 복사에너지를 정의하는 양으로 태양상수(solar constant)가 있다. 태양상수란, 태양과 지구와의 거리가 1AU일 때 지구 대기 상단에서 입사 방향으로 수직 입사하는 단위면적당 단위시간의 태양 에너지양으로, 인공위성에 의한 측정 결과에 따르면 그 양은 약 1.4kW/㎡이다. 이 태양에너지는, 약 30%가 지표면에 의한 반사나 대기 중에서의 산란, 구름에 의한 반사에 의해 우주공간으로 돌아간다. 나머지 약 70%는 지표에 도달하는 태양에너지가 되며, 그 양은 약 1.0kW/㎡이다.
지표에 도달하는 복사에너지는 파장 범위 0.2~2.0㎛의 단파 복사로서 파장이 짧은 γ선과 x선부터 자외선, 가시광선, 적외선 및 파장이 수 m에 달하는 전파까지 전자기파로 이루어져 있다. 태양방사의 파장별 에너지를 그림 3에 나타내었다.
2. 여름철 폭염 및 차량 실내 온도
절기상의 입추는 이미 지났지만 폭염의 기세는 좀처럼 꺾이지 않고 대한민국 전체가 찜질방이 된 듯한 느낌이다. 우리나라 자연 계절에 관한 연구에 의하면, 가을이 시작하는 시점은 최고기온 25℃ 이하로 정의하고 있는데 아직 멀기만 하다. 이러한 더위는 밤낮을 가리지 않아서, 낮에는 연일 30℃ 이상의 폭염 경보가 뜨고, 밤엔 그 열기가 식지 않아 열대야 현상에 시달리고 있다. 이러한 더위에 의해 열사병과 같은 온열 질환이 발생하여 어지럼증, 두통, 피로감 등의 건강 문제로 위협을 받는다.
또한, 자동차 역시 열에 상당히 취약한 특성이 있다. 특히 밀폐된 차 안은 불가마를 방불케 하는 높은 온도로 한낮 차량의 실내온도는 외부 온도의 2~3배까지 상승한다.
외부 기온이 30℃일 경우, 실내는 무려 90℃까지 상승하는 것이다. 교통안전공단에서 여름철 외부 기온에 따른 자동차의 실내온도를 측정한 결과, 한여름 기온 35℃인 상태가 4시간 지속될 때 자동차의 평균 실내온도가 70℃ 이상으로 올라가고, 앞 유리 부근의 실내온도는 무려 92℃, 뒷유리 부근은 78℃, 조수석과 뒷좌석은 62℃까지 올라갔다. 더욱이 하절기에는 어린이 실내 방치 사고 예방과 함께 인화성 물질의 제거도 상당히 중요하다.
교통안전공단의 실험에 따르면, 여름철 실외에 장시간 주차했을 경우 일회용 라이터와 캔 음료 등을 올려놓고 실험한 결과, 대시보드 온도는 92℃까지 상승했고 라이터는 82℃, 캔 음료는 78℃에서 폭발했다. 이 밖에도 뜨겁게 달궈진 실내 내장재로 인한 화상 사고와 인화성 물질을 비롯해 전자기기 내부에 장착된 배터리의 폭발 우려도 있다.
3. 창유리에 열 차단 필름 부착의 필요성
우리나라 기온은 뚜렷한 사계절에서 여름 겨울이 봄 가을 대비 상대적으로 길어지고 여름철에는 폭염으로 인해 냉방을 위한 에너지 소비의 감소를 위해 열 차단 필름이 더욱 요구되고 있다. 이러한 열 차단 필름은 창유리에 부착함으로써 차열 기능 외에도 다음과 같은 여러 가지 효과를 부여하고 있다.
(1) 냉방효율 향상에 따른 에너지 절감 효과
건물의 창유리에 열 차단 필름을 적용하면, 태양열의 40~80%를 차단할 수 있다. 이에 따른 여름철 냉방비용을 약 10~30%까지 절감할 수 있다는 연구 결과가 있다. 이는 내부 온도를 최대 2~5℃까지 낮추는 효과를 가져와, 냉방장치의 사용을 줄이는 결과를 가져올 수 있다.
미국 에너지부(DOE)의 보고서에 의하면, 고기능 열 차단 필름을 사용할 경우, 상업용 건물의 연간 에너지 비용을 최대 19%까지 절감할 수 있다고 한다. 또한 영국의 연구 결과에 의하면, 열 차단 필름의 부착으로 건물의 총에너지 사용량을 7~15% 감소한 보고도 있다.
이러한 데이터는 열 차단 필름이 에너지 소비가 많은 상업용 건물에서 더 큰 에너지 절감 효과를 가져올 수 있다는 것을 나타내고 있다.
(2) UV 차단에 의한 실내 인테리어 보호
자외선은 그 강한 에너지에 의해 피부에 해로울 뿐 아니라, 실내의 인테리어나 소파와 같은 가구에 장기간 반복 노출하면 변색을 일으킨다. 또한 차량 내부의 시트나 대시보드에도 손상을 일으키게 된다. 열 차단 필름은 일반적으로 99% 이상의 UV 차단 기능을 하고 있어서 태양광의 UV에 의한 손상을 최소화할 수 있다.
(3) 사생활 보호 효과
아파트나 상가의 용도 외에도, 자동차는 개인 프라이버시가 요구되는 장소로서, 차량 내부에서의 모습이나 행동을 보호받고 싶어 한다. 열 차단 필름은 여러 가지 색상 부여로 적절한 가시광 투과율을 조절함으로써 사생활 보호 효과를 부여하고 있다.
(4) 비산 방지 효과
지진이나 강한 태풍과 같은 자연재해에 의한 창유리의 파손뿐만 아니라, 차량을 운전하다 보면 사고 등의 이유로 창유리가 파손, 외부침입에 의한 파손, 외부에서 날아온 아스팔트 파편 및 돌멩이 칩에 의해 전면 유리가 손상되기도 한다.
창유리에 열 차단 필름을 부착하는 것만으로도 깨진 유리 파편의 비산을 방지하며, 차량의 유리가 파손되었을 때 잘게 부서지도록 설계된 자동차 유리 조각들을 필름이 잡고 있는 역할을 하게 된다.
(5) 건축적, 세련된 효과
외벽이 유리로 마감되는 건축 트랜드 변화와 우리나라의 대표적인 주거공간인 아파트의 발코니 확장 등의 공간변화로 인해 여러 가지 색상이 들어있는 열 차단 필름의 필요성이 증가하고 있다.
또한 차량의 경우, 창유리에 색상을 부여하여 외관을 한층 더 세련되고 고급스럽게 꾸밀 수 있게 해주고 있다,
(6) 눈부심 방지 효과
자동차 운전 시에 태양 빛이나 다른 차량의 헤드라이트 빛이 강할 때, 열 차단 필름에 색상이 부여되어 있으면 시야 확보가 더 쉬워진다. 하지만 너무 진한 색상은 터널 안에나 야간과 같은 어두운 곳에서는 오히려 시야 확보를 방해하기 때문에 적절한 농도를 선택하는 것이 중요하다.
4. 열 차단 필름의 시장 규모
인터넷 검색 자료이기는 하지만, 세계 열 차단 필름 시장 규모는 지난 2023년에 22억7천만 달러로 평가되었으며, 2024년 24억1천만 달러에서 2032년까지 39억9천만 달러로 성장하여 예측기간 동안 6.5%의 CAGR을 나타낼 것으로 예상된다.
건축용 윈도우 필름은 유형에 따라 NIR/UV 차단 필름, 장식용 필름, Safety 필름, 프라이버시 필름 등으로 구분할 수 있다. 지난 2021년 Global Architectural Window Film의 마켓 share는 선팅 필름이 대략 절반이고, 그다음 장식 필름, Safety&Security 필름, Privacy 필름의 순으로 차지하였다.
한편, 윈도우 필름의 용도에 따라 건축 건물용, 자동차용, 해양 및 기타용으로 분류할 수 있다. 이 중 건축 건물용이 예측기간 동안 가장 빠른 CAGR로 성장할 것으로 예상된다. 그리고 자동차용은 향후 전기자동차에 대한 수요의 증가와 각 주요 국가의 정부 규정에 따른 자동차산업의 시장 성장에 따라 달라질 것으로 예측된다.
5. 열 차단 필름의 종류 및 구조
컬러를 부여하여 선팅(혹은 틴팅) 필름이라고도 하는 열 차단 필름은 그 재료와 구조에 따라 매우 다양하게 제품이 출시되어 있으며, 하기의 표 1과 같이 분류할 수 있다.
상기의 분류는 재료, 컬러 및 기능 구현을 위한 기본적인 분류이며, 실제 판매되고 있는 제품은 2종류 이상을 합지하여 훨씬 다양한 제품들이 출시되고 있다.
하기의 그림 10은 2 ply 제품의 구조 예이다. 별개의 기능을 가진 2매의 PET 필름을 합지한 제품으로 점착층에는 시공 전에 분리하는 이형 필름이 합지되어 총 3매의 필름구조로 되어 있다.
6. IR 흡수재료
대표적인 투명 적외선 흡수 재료로 산화인듐(ITO: Indium Tin Oxide)이나 안티몬이 첨가된 산화주석(ATO: Antimony doped Tin Oxide) 등이 알려져 있으며, 보다 강력한 흡수기능을 가진 세슘-텅스텐옥사이드(CTO: Cesium dopped Tungsten Oxide)가 있다.
CTO는 페로브스카이트(Perovskite) WO₃ 구조를 가진다. Perovskite는 러시아 과학자 페로브스키를 기념하여 명명한 큐빅AMX₃의 구조체(A와 M은 양이온, X는 음이온)로 부도체, 반도체, 압전성질을 가지며, 유·무기물과 결합하여 높은 에너지 전환효율(20.1%)로 태양전지용 재료로도 연구되고 있다.
IR 복사 및 전기 전도성이 우수하고, dopant를 첨가한 Perovskite 산화물 구조를 가진 입자에 대한 연구도 활발하게 진행되고 있다.
Perovskite 산화물에서 산소의 이동속도는 빛 흡수, 전기 전도성과 같은 재료의 성질에 큰 영향을 미친다. 전자와 산소 이동성의 조합에서, 재료 성질의 향상을 위하여 산소 이온의 확산 속도를 증가시킬 수 있다. 즉, A나 B와 원자가가 다른 원소로 doping 하면 기존 산소의 site가 비거나 새로운 산소가 들어와 산소결함의 농도가 높고 이동속도가 높아져 산소확산 속도가 빨라진다. BO₃(금속산화물)의 A-site에 dopant 원소를 첨가하여 다양한 특성을 가진 입자를 형상할 수 있다.
일반적으로 tungsten oxide(WO₃) 중에는 유효한 자유전자가 존재하지 않아 IR 영역의 흡수 특성이 낮고 IR 흡수제로서 유효하지 않다. 이에 따라 IR 흡수에 특히 유효한 W와 O의 조성범위를 연구하고, WO₃에서 산소의 비율을 3보다 작게 하여 자유전자를 생성시켰다.
산소량의 제어는 WyOz에서 y에 대한 z의 비율을 2.45 ≤ z/y ≤ 2.999로 조절하여 IR 흡수를 높이고, 더욱이 자유전자를 생성하는 원소를 첨가하여 IR 흡수 효율을 더욱 향상시켰다. dopant로는 알카리금속, 알카리토금속, 희토류 원소인 Cs, Rb, K, Ti, In, Ba, Li, Ca, Sr, Fe, Sn 등을 검토하였으며, 이온반경이 큰 원소(M)를 첨가했을 때 육방적의 결정이 형성되기 용이했다.
IR 흡수 파장의 경우, 입방정 < 정방정 < 육방정의 결정구조로 갈수록 IR 흡수가 장파장으로 shift하였고, 가시광 영역에서는 반대로 육방정 < 정방정 < 입방정일수록 흡수성능이 낮아 육방정 구조가 가장 유효한 구조인 것을 확인하였다.
세슘-텅스텐옥사이드(CTO: Cesium dopped Tungsten Oxide)의 경우, 스미토모금속광산(SMM)에서는 CWO (Cs0.32WO3-y) 나노입자를 출시하고 있다. 세슘-텅스텐 산화물인 Cs0.32 WO3의 결정구조를 그림 13에 나타내었다.
이 재료는 P6₃/mcm 공간군을 가지며, c축 방향에서 투영하면 텅스텐(W)과 산소(O)에 의한 WO₆ 팔면체가 육방정의 골격을 형성하고, 그 중심에 세슘(Cs)이 위치한다(그림 13(a)). a 축 혹은 b 축 방향에서 투영하면 Cs-O(1) 면과 W-O(2) 면이 교대로 적층된 구조를 가지고 있다(그림 13(b)).
최근 이 재료의 적외선 흡수 밴드에 대한 결정의 이방성 및 입자의 불균일성을 고려한 Mie의 이론에 근거한 해석 및 제1 원리 계산에 의한 해석이 있으며, 그중에서 Cs와 산소 결함(VO)으로부터 W-5d 궤도에 공급되는 전자는 국소 표면 플라즈몬 공명(LSPR) 흡수나 폴라론(Polaron) 흡수를 담당하는 것으로 나타났다. 최근에도 전자에너지 손실 분광법(EELS)에 의한 연구 등 적외선 흡수기구의 규명을 위한 여러 가지 연구가 진행되고 있다.
Cs0.32WO₃ 입자를 만들 수 있는 다양한 제조 방법이 있으며 고상법, 수열합성법, 플라즈마법, 화염법 등이 보고되어 있다. 이들 제조 방법에 따라 분말 특성이 다르며, 투명적외선 흡수재료로서 성능에 영향을 미치는 정도도 차이가 나는 것으로 알려져 있다.
CWO의 양산공정에는 고상법이 사용되고 있으며, 원료를 소성한 후에 몇 시간 이상의 분쇄처리가 이루어지고 있다. 얻어지는 입자는 100㎚ 이하의 범위에서 여러 가지 크기 및 형상을 가지고 있으며, 이러한 편차는 폭넓은 파장의 적외선 흡수기구에 기여하기 때문에 투명적외선 흡수재료로서 실용성을 높인다.
그림 14에 900°C와 1,200°C의 전기가열로를 사용한 분무 열분해법에 의해 합성된 Cs0.32WO₃ 입자의 SEM 이미지를 나타내었다. 일반적으로 분무 열분해법으로 합성되는 입자는 액적의 크기와 입자 농도에 기인하여 서브 미크론 크기의 입자를 얻을 수 있다.
그러나 재료에 따라서는, 생성한 서브 미크론 크기의 입자가 고온에서 승화하고, 생성한 응축성 물질이 반응관의 출구 부근에서 급격하게 냉각되어 나노입자를 얻을 수 있는 것이 알려져 있다. Cs0.32WO₃ 입자의 경우도 기상 가열온도가 1,000°C 이하인 경우는 서브 미크론 크기의 입자를 얻을 수 있지만(그림 14(a)), 1,200°C 이상으로 함으로써 거의 모든 생성된 입자의 나노화가 가능해졌다(그림 14(b)).
Cesium이 doping 된 WO₃ 입자를 수열 합성법으로 제조한 Cs0.33WO₃ 입자의 제조법 예를 조사하였다.
Tungstic acid 입자의 제조는 Tungstic acid 용액의 고분자화 과정에 이루어진다. 전구체 물질로 Sodium tungstate solution(Na₆O39W12H₂O)을 수용 액상에서 제조하고, 양이온 교환수지를 통과시켜 Na를 치환하고 투명한 노란색의 Tungstic acid 용액을 얻는다. 그리고 일정 시간 방치, 원심분리로 불투명 노란색 입자를 침전하여 Tungstic acid 입자를 제조한다.
제조된 텅스텐 산화물 입자는 구연산에 분산하고 Cesium을 첨가하여 120~180℃ 수열 합성하여 진남색의 물질을 얻고, 세척과 진공 건조하여 세슘-텅스텐 산화물을 제조한다. 그 과정을 그림 15 및 그림 16에 정리하였다.
이와 같이 제조된 Cs0.33WO₃ 입자는 나노 분산기에서 수십 ㎚의 크기의 sharp한 입도로 분산시키고 도료화하여 입자의 첨가량별 파장별 IR 흡수 특성을 확인할 수 있다.
한편 dopant 물질인 Cesium의 CsxW₁O₃ 입자의 Cs 비율에 따른 1,000㎚ 파장에서의 흡수율이 보고되어 있다. Perovskite 산화물은 ABO₃의 구조를 가지며, 합성된 CsxW₁O₃ 입자의 구조 control을 위해 heat annealing 온도는 700~900℃ 범위 중, 800℃가 흡수율에 최적이었다. 가시광 투과율을 위해 입자 크기는 수십 ㎚ 이하로 유지하였고, binder는 빛에 의한 yellowing을 최소화하기 위해 silane계 무기 binder를 사용하였다.
Cesium의 mol 수 0.33, 0.5, 0.75, 1.0에 따라 4종의 CsxW₁O₃(Cs0.33W₁O₃, Cs0.5W₁O₃, Cs0.75W₁O₃, Cs1.0W₁O₃) 입자를 제조하여 평가하였다. 그 결과, 그림 18에서 보듯이 Cs0.33 W₁O₃에서 최대 흡수를 확인하였다.
스미토모금속광산(SMM)의 보고(Near Infrared Absorption of Tungsten Oxide Nano particle Dispersion, 2007)에 의하면, 텅스텐옥사이드(WO₃)의 band gap은 2.62eV이고, 가시광(380~ 780㎚)과 NIR 영역(780~2,100㎚)에서 투명하다.
앞에서 서술한 바와 같이 NIR의 흡수는 O₂ 성분의 감소, 3번째 성분의 doping에 따른 free electron의 금속 내 도입에 의해 유도로 기능이 발생한다. 산소의 결핍은 Magnéli 구조인 complex-ordered 구조를 형성하는 반면, +이온인 3번째 성분의 도입은 tungsten bronze 구조를 만든다.
합성된 powder 크기(0.5~5.0㎜)를 filler/분산제/toluene=8/8/84의 비율로 0.3㎜ 지르코니아 beads가 충진된 paint shaker mill을 사용하여 6hr동안 나노 분산하여 particle size 50~100㎚(1차 입자 크기 20~30㎚)를 얻었다.
그 결과, 그림 19에서 보듯이 WO₃의 환원에 따른 파장별 빛의 흡수영향을 확인하였다.
환원된(reduced) Tungsten oxide는 가시광과 NIR 영역에서 broad한 흡수를 하지만 O₂의 감소에 따라 ① 가시광 영역에서 투과율 감소, ② main 흡수는 단파장 쪽으로 shift의 결과를 보이고 있다. 그리고 1,620~ 1,700㎚에서의 disturbance는 용매로 사용한 toluene에 의한 영향이다. 이러한 결과로 Tungsten oxide bronze(MχWO₃)는 강한 NIR 흡수를 이끄는 것을 알 수 있다.
한편 입자 size의 감소에 따라 가시광 영역에서는 scattering을 감소시켜 높은 투과율을 보이지만, NIR 영역에서 nano particle의 total 개수가 많아지기 때문에 흡수가 증가한다 (absorption >> scattering).
그림 20에서 보듯이 Dopant 물질의 도입에 의해 MχWO₃의 HTBs(hexagonal tungsten bronze) Ti, Rb, Cs, Na는 NIR 영역에서 강한 흡수를 보이고 있다. Na의 경우 가시광 영역에서 다른 물질에 비해 투과율 감소의 경향을 나타낸다.
한편 시중에서 일반적으로 사용되고 있는 ATO(antimon tin oxide)와 CTO(cesium doped tungsten oxide)의 입자 첨가량에 따른 투과율의 변화를 그림 21에 나타내었다.
ATO 졸의 경우 비교적 장파장(1,500~2,500㎚) IR 영역에서 우수한 흡수 효과를 보이는 반면, CTO 졸은 NIR(1,000~2,000㎚) 영역에서 양호한 흡수기능을 가지고 있다. 재료의 가격 면에서도 ATO 졸이 CTO 졸의 30% 수준으로 낮기 때문에, 선팅 필름의 IR cut 설계에서는 일반적으로 CTO 졸과 ATO 졸을 혼합 사용하여 측정 가능한 IR 영역(~2,500㎚)의 모든 파장에 걸쳐 효과적인 흡수기능을 부여하고 있다.
또한 단일 파장(1,000㎚) ATO 졸과 CTO 졸의 함량별 흡수율을 조사하였다. 그림 22에서 NIR 열선의 주요 파장(950~1,400㎚)에 있어, 두 입자의 흡수 특성에 기인해 ATO 졸은 함량을 늘려도 50% 정도의 흡수에서 수렴하는 반면, CTO 졸은 97.5% 정도까지 상승하는 것을 볼 수 있다. 이를 통해 가성비를 고려한 적정한 비율의 formulation 설계가 가능해진다.
7. IR 흡수 입자의 나노 분산
IR 흡수 입자는 1차 입자 크기(수십 ㎚)로 binder 내에 균일하게 분산되어 있어야 한다. 입자가 뭉쳐 있을 경우, haze 상승, NIR 흡수 저하, sparkling 외관 불량을 유발하고 시인성이 떨어져 열 차단 필름의 상품 가치가 저하된다.시판 중인 ATO size는 30~50㎚ 정도이며, 그 입자 분포도 그림 23에서 보듯이 sharp한 형상을 보이고 있다.
분산은 그림 24와 같이 3단계의 과정을 거쳐 표면 젖음, 기계적 해쇄, 분리된 입자의 안정화 상태를 만든다.
nano particle은 제조공정에서 많은 에너지를 가하여 생산하기 때문에, 제조된 입자는 표면에 쌓인 에너지를 가지고 있으므로 통상 수백 ㎚~수 ㎜ 정도의 크기로 응집하여 상온에서 안정을 유지하려고 한다.
그러므로 particle은 1차 입자 사이에 공기층을 두고 분자인력에 의해 면 접촉하며 강하게 흡착하고 있다. 이를 효과적으로 분리하기 위해서는 먼저 ① 용매(solvent)를 사용하여 공기층을 밀어내 대체하여 입자의 표면을 wetting시키고, ② 입자 사이를 분리할 수 있는 기계적인 강한 원심력과 beads 충격력에 의해 기계적 해쇄를 하며, 마지막으로 ③ 분산제를 사용하여 분리된 입자 사이에 입체적 장애를 만들어 다시 응집하지 않고 일정 기간 분리된 상태를 유지시킨다.
이렇게 분산 안정된 도료는 일정 기간 후에 재료의 비중 차이에 의해 침전이 생기고, 재응집이 발생해도 선 접촉 혹은 점 접촉에 의해 약하게 연결되어 있기 때문에 가벼운 교반만으로도 다시 초기의 분리 상태로 회복할 수 있다.
많은 유형의 분산장치가 시판되고 있으며, 나노 분산에는 주로 폐쇄형 disk bead mill이 사용되고 있다. 일반 disk mill과 비교하여 나노 분산기의 특징은 ① 도료와 beads의 분리 방식, ② 충진 beads 크기이다.
일반 disk mill의 경우, 토출구에서 beads 분리를 위해 mech seal 또는 screen을 사용한다. 일반적인 도료는 1.0~2.0㎜ 정도의 zirconia 및 glass beads를 사용하지만, nano particle에는 sub-micron 크기를 사용하기 때문에 이를 효과적으로 분리해내기 위해 원심분리 방식의 분리기가 적용되고 있다. 더욱이 1990년 중반의 1회전 축(disk 회전+원심분리)을 좀 더 개선한 2축 분리된(disk 회전과 원심분리 회전축 별개) 2세대 나노 분산기가 2008년 출시되어 널리 사용되고 있다.
nano particle의 분산에 사용되는 beads는 수백 ㎚ 크기이다. 이는 예를 들어 쌀알을 분리시키기 위해 축구공과 골프공으로 부딪쳐 충격을 가할 때, 비 표면적 충돌의 기회가 어느 쪽이 더 효과적인지 이미지로 비교하면 이해가 가능할 것이다.
8. IR 흡수 금속 막(증착, 스퍼터링)
코팅 가공기술 중 금속 막을 형성시키는 증착과 스퍼터링의 기본적인 구조와 코팅 방법에 대해 비교를 하고자 한다.
증착은 진공 속에서 물질을 증발시켜 성막 하는 방법으로 스퍼터보다 이전부터 실용화되어 사용되어 왔다. 진공 챔버 내에서 재료가 되는 물질에 저항 가열, 전자빔, 고주파 유도, 레이저 등에 의한 열에너지(10-1~10-2eV)를 가해 재료를 증발시켜 기판(필름)에 막을 형성하는 기술이다.
증착 물질을 기화시키는 방법에 따라 가열하여 기판에 부착하는 Thermal Evaporation과 전자빔으로 기화시키는 E-beam Evaporation으로 나눌 수 있으며, E-beam 증착이 국소적으로 높은 온도를 가할 수 있기 때문에 비점이 높은 물질에도 가능한 장점이 있다.
스퍼터링은 진공 속에서 음극(target)에 전압을 가하면 양극(기판, 필름 등) 사이에 전기장이 형성되고, 이 전기장에 노출된 아르곤(Ar) 가스가 Ar+로 이온화되면서 양극-음극 사이에 플라즈마(plasma)가 발생한다.
Target 물질의 표면이 음전위로 유지되므로 Ar+가 target 표면에 가속하여 충돌하고, target 물질이 표면으로부터 방출되어 기판(필름)으로 날아가 막을 형성하게 된다.
스퍼터링은 재료에 운동에너지(102~103eV)를 가하여 증착에 비해 복잡한 합금층을 유지하는 능력이 뛰어나고, 막응력이 높으며 금속의 고온 내열성이 우수하다. 스퍼터링 공정의 수율은 충돌 이온의 입사각, target 물질의 조성, 충돌 이온의 종류, 이온의 에너지 등에 의해 영향을 받는다.
열 차단 필름을 제조하기 위해 스퍼터링 공정은 multi target을 사용하여 단층~다층 막을 형성하며, 생산성 향상과 cost 절감에 기여한다. 다층 설계는 주로 Ag층을 형성할 경우 산화 방지를 위해 상하의 보호층으로 금속 산화물(metal oxide)층을 적층하여 성막한다. 또한 내구성 향상을 위해 Ag층도 단층이 아닌 복수의 층을 구성하기 때문에 적게는 몇 개~20여 개까지 multi target의 sputter 장치를 사용하고 있다.
열 차단 필름의 경우 0.5~1.5mil(1mil=25㎛)의 얇은 PET 필름을 사용하기 때문에 성막 가공 시의 열특성에 민감하며, 공정에 이상이 있을 경우 열 주름이 발생한다. 또한 금속층 두께에 따라 색상 및 IR 흡수성의 변화가 있기 때문에 정밀한 operating에 의해 공정을 제어해야 한다.
니켈크롬(NiCr), 티타늄(Ti), 구리(Cu) 등과 같은 금속 성막층은 Ag에 비하여 비교적 산화 영향이 적기 때문에 가성비의 스퍼터 필름으로 널리 사용된다. 알루미늄층의 경우는 스퍼터 보다 훨씬 저렴한 증착 공정 제품이 적용되고 있다.
이들 금속층은 성막 농도(OD; optical density)가 가시광부터 IR 영역까지 거의 전 파장에 걸쳐 유사하기 때문에 가시광 투과율(VLT; visible light transmittance)과 IR 차단율(IRR; Infrared rejection)의 비율이 거의 일정하다.
Ag는 성막 층이 두께에 따라 색상도 달라지며, 가시광 영역(380~780㎚)에서 투과율이 높고 NIR 영역(950~1,400㎚)에서 투과율이 낮아지는 특성을 가지고 있어 시인성이 요구되는 열 차단 필름에 외관 및 특성 제어를 할 수 있는 매우 이상적인 재료이다.
한편, Ag 성막 층은 Ag의 두께 증가에 따라 Ag layer의 morphology가 변화하며, 그 영향으로 파장별 투과율이 달라진다. 그림 33과 같이 GZO/Ag/GZO 구조에서 Ag층의 두께가 상승함에 따라 550㎚ 파장에서의 투과율은 높아지며, 두께 12㎛에서 최대 peak를 보이고 다시 감소한다. 이러한 이유는 그림 34와 같이 Ag층의 두께에 따른 표면의 모폴로지(morphology)의 차이에 기인하는 것으로 생각된다.
두께가 낮은 경우는 Ag층이 random 배열로 밀도가 낮으며, 두께의 증가에 따라 농도가 높아지다가 12㎛에서 가장 조밀한 형상을 보이고, 그 이상의 두께에서는 rough 해지는 표면 형상에서 유래하는 것으로 여겨진다.
또한 다른 문헌에서도 AZO(30㎚)/Ag(x)/AZO(30㎚)의 구조에서, x=5, 7, 9, 10, 11, 13, 15, 17㎚ 중 10㎚에서 투과율이 max peak를 보이는 것을 알 수 있다(그림 35). 한편 Ag의 aggregation은 온도, 습도, surrounding layer에 의한 diffusivity에 의해서도 영향을 받는다.